
Precision Molding of High-Performance BMC Headlight Reflectors
iangsu Lantai (Kaerda) specializes in the precision molding of Bulk Molding Compound (BMC) headlight reflectors and reflector bowls, which are fundamental to the performance and safety of modern automotive lighting systems. Our expertise encompasses the entire reflector bowl, engineered for perfect optical precision in headlamps, fog lamps, and other vehicle lights. We utilize advanced BMC formulations, specifically engineered by Kaerda, to deliver superior thermal resistance, a flawless Class A surface for metallization, robust durability, and exceptional dimensional stability. Our manufacturing processes are designed to produce components that consistently meet the stringent photometric and aesthetic requirements of the automotive industry, ensuring brilliant light output and long-term reliability.
The integrity of Kaerda's BMC reflector bowls is paramount. Our specialized BMC materials are formulated to withstand high continuous operating temperatures from halogen, HID, or LED sources, ensuring dependable performance without deformation. These components serve as the key optical element, whose precise geometry dictates the focus and pattern of the light beam. Therefore, our focus on exceptional dimensional stability ensures they can maintain this critical geometry reliably, while their flawless Class A surface guarantees a perfect, highly reflective finish after vacuum metallization. Kaerda’s commitment to quality includes ensuring properties like high heat resistance and ultra-smooth surfaces are inherent in our BMC headlight reflectors.
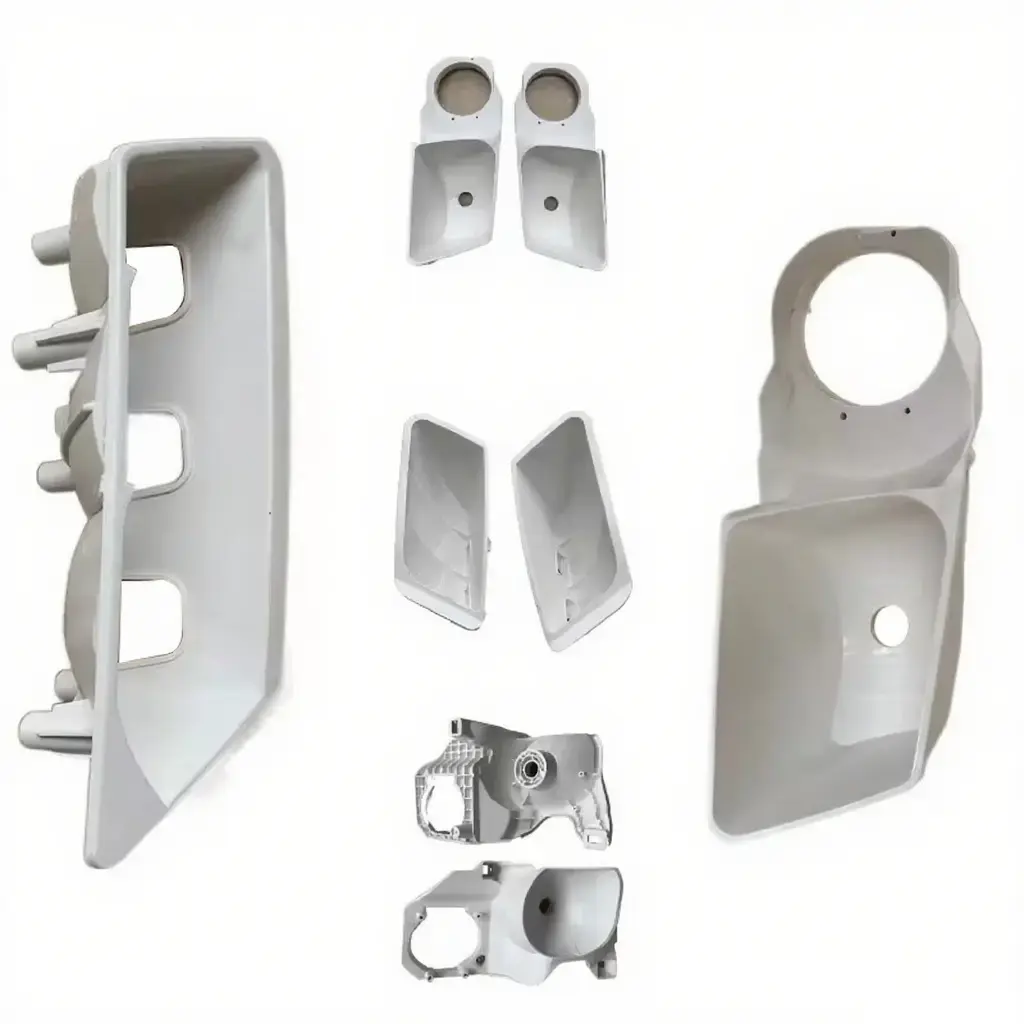
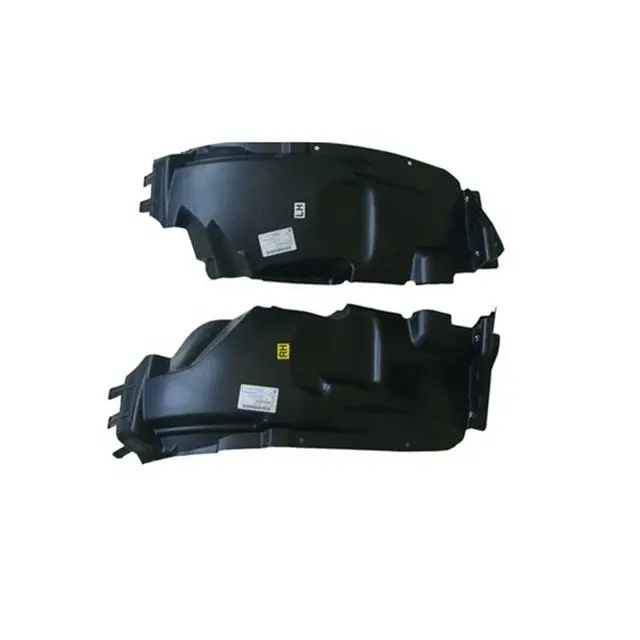
Advanced BMC Technology for Flawless Automotive Lighting Components
Kaerda (Jiangsu Lantai) employs advanced technology throughout its Bulk Molding Compound (BMC) production and molding processes to manufacture superior headlight reflectors. Our facilities are equipped with 7 sets of specialized BMC production equipment and a versatile array of 16 different tonnage molding machines, suitable for both compression and injection molding techniques. This robust infrastructure enables the efficient, high-volume production of diverse and often intricate reflector bowl geometries essential for modern lighting performance. Our automated controls in BMC compounding ensure homogenous material properties critical for consistent thermal resistance and surface quality, while advanced molding techniques allow for the precise replication of complex parabolic shapes and tight dimensional tolerances, ensuring each part meets the high-performance criteria of the automotive industry.
Material Stability
Dedicated BMC compounding facilities utilizing 7 equipment sets to ensure optimized material properties for high-heat automotive lighting environments.
Optical Precision
High-precision molding capabilities leveraging our 16 diverse presses for complex reflector geometries and consistent, flawless surface quality.
Expert Design & Material Solutions for Custom Headlight Reflector Needs
The performance, safety, and aesthetic appeal of modern vehicle headlamps depend fundamentally on the quality and design of their reflector bowls. Kaerda (Jiangsu Lantai) offers extensive expertise in designing and manufacturing custom BMC solutions that precisely address these critical demands. Our R&D and engineering teams collaborate closely with automotive lighting manufacturers, understanding the nuances of photometric requirements and the specific performance needs of the headlight reflector. We develop tailored BMC formulations to optimize characteristics such as thermal management (withstanding high heat), optical precision (dimensional stability for beam focus), surface quality (flawless Class A for metallization), and lightweighting. This collaborative and solutions-driven approach ensures that Kaerda's BMC reflector bowls provide a robust, reliable, and precisely engineered foundation for the brilliant and safe operation of your vehicle lighting systems.